Waterproof Concrete Staten Island is an investment that ensures the integrity of your structure. It protects the structure against moisture and dampness that causes mold and mildew to form, which affects both the aesthetic and the health of people who use the building.
Waterproof concrete can be created by incorporating a special admixture into fresh concrete. There are several benefits to this approach:
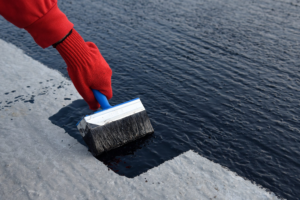
Waterproof concrete is an economical choice that saves money on maintenance. This is because it protects the internal materials from attack by moisture and prevents erosion, which can cause damage to electrical work or paint jobs. It also helps to keep the structure looking good and adds value to property.
Waterproof cement is manufactured using various agents to resist water and moisture. It is often used in residential foundations, basements, water tanks, swimming pools, roofing and RCC foundations. Concrete with this coating is usually stronger and more durable than ordinary concrete. It also resists cracking and can withstand harsh weather conditions.
Xypex is a concrete admixture that makes the concrete waterproof, eliminating the need to apply a separate coating or sealant. The admixture is added during the mixing process and can be used for new construction or repair projects. It is cost-effective, easy to use, and does not require any special skills or training to install. It also reduces the amount of concrete required for a project, allowing contractors to meet project budget and schedule constraints.
The advantage of waterproof concrete is that it protects the re-bar and other internal materials in a concrete structure. This is important because corrosion of steel and deterioration of concrete can lead to the loss of structural integrity. Xypex can help to extend the life of a building or other concrete structure and reduce maintenance costs by keeping it dry and preventing water damage.
Another advantage of waterproof concrete is that it can help to combat mold and mildew, which can be a health hazard for people living in the structure. Moisture can also cause a build-up of fungus that is harmful to plants and animals. Xypex can protect against this build-up and ensure a clean, healthy space for people to live in.
Waterproofing concrete is a worthwhile investment in any concrete project. It can reduce maintenance costs, prevent structural damage and improve the appearance of the finished product. It can also increase the value of a home or other concrete structure, as prospective buyers will be more likely to buy it if it is waterproof.
Durability
Waterproofing is a critical component of building construction. When not properly done, a building will experience water seepage that can lead to costly repairs and unusable space. To avoid such problems, it is recommended that a waterproofing system be applied to concrete and cement-based surfaces during construction or renovation.
One such waterproofing solution is the use of specialized admixtures that reduce concrete permeability. These admixtures are added to the concrete mix during mixing or directly to the hopper of the concrete truck at the jobsite. These admixtures work by chemically reacting with the water and unhydrated cement particles to create millions of tiny needle-like crystals that fill capillary pores and micro-cracks, blocking the pathways for water to penetrate the structure.
This method of waterproofing is highly effective and also very cost-efficient compared to other methods, such as spray-on membranes. Additionally, it is more durable than other methods because the crystalline crystals remain permanently embedded in the concrete matrix. This is important because it prevents the occurrence of leaks and dampness that can cause mold growth, damage to the substrate and the structure, and even loss of performance.
As a result, the crystalline crystals can last for the lifetime of the building. This makes waterproofing an excellent choice for residential and commercial buildings alike.
For a commercial project, crystalline waterproofing is an excellent option because it protects the building from the effects of long-term exposure to moisture and can even save on energy bills by reducing humidity levels. For a residential project, crystalline waterproofing is an excellent choice for preventing foundation cracks and dampness. This can help prevent mold growth, musty odors, and damage to the floor and walls that can result in costly repair and replacement.
A homeowner in Staten Island, New York, noticed that the concrete sidewalks around his home were sinking and settling causing tripping hazards. After searching the web for solutions, he found Quality 1st Basement Systems and requested a quote for a PolyLevel System.
After the installation of the system, the walkways were leveled and no longer tilted. This prevented tripping and tripping accidents, and improved safety. The customer was happy with the results and referred the company to his family and friends.
Aesthetics
Whether your concrete surface is for outdoor patios, swimming pools, basements, or any structure that is exposed to moisture, the use of waterproof materials can significantly reduce maintenance and repair costs. It also prevents the build-up of mold and mildew, which are not only unsightly but can impact the health of anyone occupying the space.
As the premier concrete contractors Staten Island residents rely on, HiTek offers numerous concrete repair and restoration services. One example is French Drain Installation, which redirects surface water and groundwater away from foundations, safeguarding them against structural damage.
Another service is CTi’s Acrylistain system, which combines the rich aesthetics of concrete stain with the durability of a hard-wearing protective coating. The Acrylistain system is an environmentally friendly alternative to acid stained concrete, and it comes in a wide variety of colors to match any design style.
Located across the Verrazzano Narrows Bridge from Manhattan, Staten Island’s suburban character and sense of community make it a unique New York City borough. The area is renowned for its natural beauty, featuring parks like the Staten Island Greenbelt and the Snug Harbor Cultural Center and Botanical Garden. Its waterfront scenery and easy access to Manhattan provide opportunities for boating, fishing, and other outdoor activities.
Health
Waterproof concrete is made of cement mixed with a mixture of aggregates and water. The curing process sees this concrete mix become stronger and denser, as it absorbs the water. However, this doesn’t mean that the concrete is completely waterproof. In fact, the concrete is still able to absorb moisture and dampness can be a big problem for concrete structures. Luckily, waterproof concrete can be created by adding special ingredients into the mix. These additives help prevent moisture from penetrating the concrete, meaning that you can enjoy the durability of concrete without worrying about the health risks associated with it.
Moisture build-up in the ceiling and walls of a building can lead to serious health problems for those that live there. This is because the moisture can encourage the growth of fungus or mould, which can cause a wide range of health issues, including asthma and a weakened immune system. If this is left untreated, it can also lead to the structural deterioration of the building – which can be costly and difficult to repair.
By having a fully bonded waterproof membrane installed in the concrete, you can ensure that any leaks are prevented from migrating laterally. This can save you a lot of time and money down the road, as it means that you won’t have to spend so much time trying to repair your concrete structure.
A leaking basement is a major problem that can cause your home or business to suffer from water damage. The damage can be very costly and you may need to replace your flooring, walls, furniture and other valuable items. Waterproofing the concrete in your basement can prevent this from happening and will make your space a safer place to work or live.
If you’re looking for a reliable concrete contractor, look no further than PolyLevel. This innovative concrete leveling system can lift sunken concrete slabs in your Staten Island home and boost curb appeal. Unlike traditional mudjacking methods, which can be expensive and messy, PolyLevel is a cost-effective, non-invasive alternative. To learn more about our services, contact us today.